Dans cette seconde section, nous discuterons des opérations possibles en matières d’usinage ainsi que des caractéristiques des outils de coupe.
En un rien de temps tu seras incollable sur :
Opérations possibles
Opération | Illustration | Description |
Le fraisage en bout |
|
Le fraisage en bout est l’opération la plus utilisée sur une fraiseuse. Elle consiste à retirer de la matière… avec le bout de la fraise! La fraise ressemble alors beaucoup à un forêt à bout plat. En combinant des déplacements axiaux et radiaux, il est alors possible de créer toute sorte de géométries. Une routine d’usinage utilisera généralement plusieurs grandeurs de fraise différentes afin de créer la géométrie finale. |
Plonger avec une fraise? |
![]() ![]() |
Contrairement au foret utilisé pour percer, il n’est pas toujours possible de « plonger » dans la pièce à usiner (illustré en (a) ci-contre). La raison derrière ce comportement est que le centre de la fraise peut ou ne peut être muni de surfaces coupantes. L’image de gauche illustre la différence entre une fraise muni d’un centre coupant ou non. Une fraise à centre non-coupant ne peut être utilisée dans un mouvement purement axial. Il faudra alors avoir recours à un déplacement combiné (axial et radial) comme une rampe (illustré en (b)) ou encore une hélice (illustré en (c)). |
Le fraisage en surface |
![]() ![]() |
Le fraisage en surface utilise généralement un outil beaucoup plus large, mais restreint à des profondeurs de coupe faible afin de retirer de la matière sur une grande surface. Ce type d’opération est souvent utilisé au début d’une routine d’usinage afin de ramener la forme brut de la matière à des dimensions connues. |
Le perçage |
![]() |
Le perçage est l’opération la plus efficace afin de retirer de la matière en terme de volume de matière retiré par période de temps. Elle consiste en un simple déplacement axial de l’outil. Lors d’une utilisation sur une fraiseuse, l’outil sera en rotation et la pièce fixe mais dans le cas d’une utilisation sur un tour, l’inverse se produira. Plusieurs longueurs et diamètres de foret existent, mais leurs utilisations en reste la même. Afin de maximiser la qualité du trou produit, on choisira de percer par coupe interrompue (peck drilling) afin de faciliter l’éjection de copeaux à une profondeur de plus de 3 diamètres (D/L>3). Il est typiquement possible de percer avec un foret standard jusqu’à un ratio diamètre/longueur de 10. Au-delà de ce ratio, de l’équipement spécialisé sera nécessaire. |
Forêt à pointer |
![]() ![]() |
Un foret à pointer sert typiquement à augmenter la précision de la position du trou à percer. Ceci est spécialement vrai avec les forets de plus grand diamètre. Contrairement à la croyance populaire, la pointe d’un forêt n’est pas… pointue mais plutôt plate. Lorsque le forêt entre en contact avec la pièce à usiner, celle-ci a tendance à glisser sur la surface avant de s’enfoncer dans la matière. Ce phénomène cause donc une certaine incertitude sur la position du trou ainsi créé. Le déplacement initial du foret est d’autant plus exacerbé avec la longueur de l’outil. Ainsi, deux solutions sont disponibles afin de réduire ce déplacement de l’outil:
En quoi pointer la surface améliore la position du trou? Un forêt à pointer possède typiquement un angle de pointe de 90° et a une très faible longueur. La déflexion est alors minimale. Un forêt à percer standard possède un angle de pointe de 118°. Alors lorsque celui-ci entre en contact avec la matière, il le fait via les surfaces coupantes plutôt qu’avec la pointe. On évite alors le glissement discuté plus haut! |
Forêt à centrer ou à pointer? |
Attention de ne pas confondre le foret à pointer et celui à centrer! Le foret à centrer possède une pointe de faible diamètre et un angle typiquement de 60°. il est plutôt utilisé sur un tour afin de créer une surface sur laquelle appuyer la pointe de la poupée. Il est aussi possible de l’utiliser comme foret à centrer mais la courte pointe en fait un outil plus fragile! | |
Chariotage, dressage et profilage |
![]() |
Ces trois opérations consistent à retirer de la matière par l’extérieur (par opposition aux opérations de type alésage). L’opération de chariotage retire de la matière sur le rayon tandis que l’opération de dressage en retire sur la face avant. L’opération de profilage consiste à créer un profil complexe et est donc une opération combinant des déplacements radiaux et axiaux. Il est parfois possible d’utiliser un seul et même outil pour effectuer ces trois opérations. La seule limitation est le profil à réaliser qui obstrue parfois l’accès à l’outil de coupe. |
Rainurage et tronçonnage |
|
Le rainurage est typiquement utilisé afin de créer des profils profonds et étroits. L’outil se déplace vers l’axe de rotation de la pièce pour retirer de la matière. Dans certains cas, il est aussi possible d’utiliser un outil à rainurer afin de retirer de la matière avec des déplacements axiaux. ATTENTION: Ce ne sont pas tout les outils à rainurer qui permettent une telle utilisation. Vérifier avant afin de ne pas endommager l’outil! Lorsqu’on couper la pièce à une certaine longueur, un outil à rainurer sera aussi utilisé. En revanche, on parlera alors de tronçonnage plutôt que de rainurage. Conseil d’expérience, il est fortement recommandé de réduire la vitesse de rotation de la pièce avant de retirer les derniers millimètres la rattachant au reste du matériel. Cela évitera qu’elle ne s’envole et s’abîme! |
Alésage |
![]() ![]() ![]() |
L’alésage est une opération très similaire au chariotage mais celle-ci s’effectue à l’intérieur de la pièce. L’outil requis afin d’effectuer cette opération est donc très différent! On parlera alors d’une barre à aléser puisque l’outil est très long et en porte-à-faux. Pour cette raison, la profondeur de coupe effectuée est relativement faible puisque l’outil est long et donc sujet à une déflexion et des vibrations. Il est aussi possible d’aléser sur une fraiseuse à l’aide d’un alésoir ou d’une tète à aléser. |
Chanfrein |
![]() |
Un chanfrein est une petite surface oblique utilisée pour joindre ou relier deux autres surfaces. Un chanfrein peut être extérieur ou intérieur, et dépend de deux paramètres a et b (ou une longueur plus un angle) et permet notamment de supprimer une arête vive. |
Filetage |
![]() ![]() ![]() |
Tout les filets ne sont pas créés égaux! Il est d’une importance capitale de connaître la géométrie des filets que vous souhaitez usiner (UNC, ACME, NPT, etc). De plus, lors de la programmation, garder en tête que plus la pastille se rapproche de la profondeur finale, plus l’engagement de l’outil augmentera. La figure illustre ce concept. Cela aura pour effet d’augmenter la frictions sur l’outil résultant en de plus grands efforts de coupe et plus de chaleur. Attention à ne pas briser cette fragile pointe! Plutôt que d’augmenter le nombres de passages de l’outil, il est recommandé de:
Vous un article intéressant discutant de ce sujet sur Modern Machine Shop |
Caractéristiques des outils de coupe
Fraise
Les fraises, qu’elles soient en bout ou à surfacer, peuvent être fondamentalement définies par 3 caractéristiques: diamètre, longueur et nombre de dents. Décortiquons l’effet de ces caractéristiques sur les performances de l’outil
Nombre de dent
Le nombre de dents, ou plutôt de surfaces coupantes de l’outil, affecte directement les performance de l’outil sur deux fronts. Dans un premier temps, un plus faible nombre de dent augmente l’espace disponible entre celles-ci. Cette espace, souvent appelé « flûte », sert comme convoyeur afin d’évacuer les copeaux formés. Dans des cas où un matériau gommant serait usiné, par exemple de l’aluminium ou du plastique, il est recommandé de diminuer le nombre de dents afin d’éviter de remplir les flûtes de l’outil. Ce phénomène, appelé aussi chip welding, empêche l’évacuer adéquate des copeaux et amène donc à une défaillance prématurée de l’outil de coupe.
D’un autre côté, un faible nombre de flûtes dans une fraise impliquera généralement une aire de section réduite. Ainsi la rigidité de l’outil s’en trouvera réduite. On souhaite donc avoir le plus grand nombre de dents afin de maximiser la rigidité de l’outil utilisé. un outil trop souple sera généralement plus prompt à vibrer ou défléchir lors de l’usinage. On observera alors un fini de surface médiocre ou des pièces hors-tolérances.
Le tableau ci-après donne quelques recommandations sur le nombre de dents d’une fraise en fonction du matériau à usiner.
Matériau | n |
---|---|
Plastique | 1-2 |
Aluminium | 2-3 |
Acier | 4 et + |
Dimensions
Il est possible de ramener les dimensions de l’outil en un seul ratio: le facteur de forme (longueur/diamètre). Les outils allongés (facteur de forme > 10) seront beaucoup plus flexible et donc susceptibles à vibrer et fléchir que les outils courts. Il est donc préférable de minimiser la longueur de l’outil afin de d’éviter les désagréments expliqués plus haut. Dans le cas où il n’est pas possible d’utiliser un outil plus court, il faudra alors ajuster les paramètres de coupe. De manière générale, on choisira de réduire la largeur de coupe, réduire la vitesse d’avance, augmenter la vitesse de rotation ou une combinaisons de ces facteurs.
Forme de la tête
On retrouve typiquement 3 formes de tête tel qu’illustré ci-contre soient plate (Flat), sphérique (Ball) et arrondie (Bull nose).
La fraise plate est la plus classique et la plus utilisée. La fraise sphérique est généralement utilisée afin de créer des contours complexes en 3D.On cherchera à utiliser les côtés de la sphère plutôt que le bout puisque la vitesse de rotation y est plus importante. La fraise arrondie est un outil plus robuste que la fraise plate traditionnelle notamment en raison de l’absence de bout pointu et donc fragile. Elle pourra être utilisée de manière plus agressive ou simplement afin d’usiner un arrondi sans avoir recours à une fraise sphérique de petite dimension.
Flutes acérées
Les dents acérées permettent de réduire la taille des copeaux produits. Cela à pour effet de faciliter leur évacuation et de réduire le couple associé. Ce type de fraise laisse un fini de surface médiocre et est donc généralement réservé aux opérations de dégrossissage (roughing).
Outil à point-unique
Les outils typiques utilisés sur un tour sont dits à point-unique. C’est à dire qu’ils n’entrent en contact avec la pièce que sur un seul point. On pourrait aussi dire qu’ils n’ont qu’une seule « dent ». La seule exception à cette règle est l’utilisation de forets qui eux ont deux surfaces de coupe. Celle-ci est présentée dans la section sur la fraiseuse mais le concept reste le même. Les sections suivantes illustrent les différentes opérations classiquement effectuées sur un tour.
Matériaux et revêtements
Matériaux d’outils
Voici un tableau résumant les caractéristiques des matériaux d’outils les plus communs. Il existe plusieurs autres matériaux d’outils, par contre ils sont utilisés pour des matériaux exotiques ou très abrasifs qui ne sont pas permis au Polyfab.
Matériau | Avantages | Inconvénients |
---|---|---|
Acier Rapide (HSS) |
|
|
Acier au cobalt |
|
|
Carbure |
|
|
Revêtements
Voici un tableau résumant les caractéristiques des principaux revêtements d’outils:
Revêtement | Avantage | Application | Couleur |
---|---|---|---|
Brunissage (Black oxide) |
Application générale | Noir | |
TiN | Alliages fereeux | Doré | |
AlTin | Alliages dur et exotiques | Gris Foncé |
Porte outil
- Porte outil à vis (A)
- Porte outil à collet (B)
- Mandrin (C)
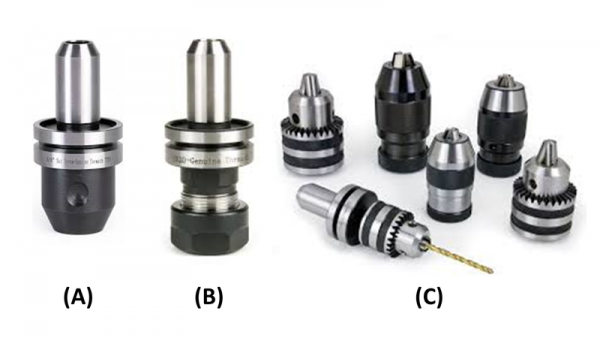
Vidéos Suggérés
Références
- [1] Churchill, W., & Roosevelt, P. (1941). Basic Definitions and Cutting Tool Geometry , Single Point Cutting Tools. URL
- [2] Vidéo sur les outils de coupe par la compagnie Tormach
Qu'as-tu retenu ? 🤔
Avant de passer à la section suivante, tu dois compléter l’examen validant cette section sur Moodlequiz.